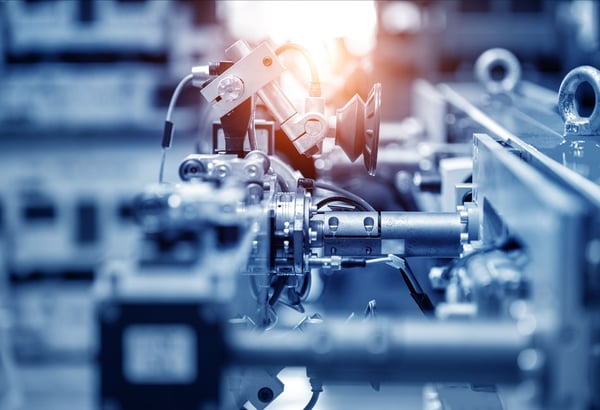
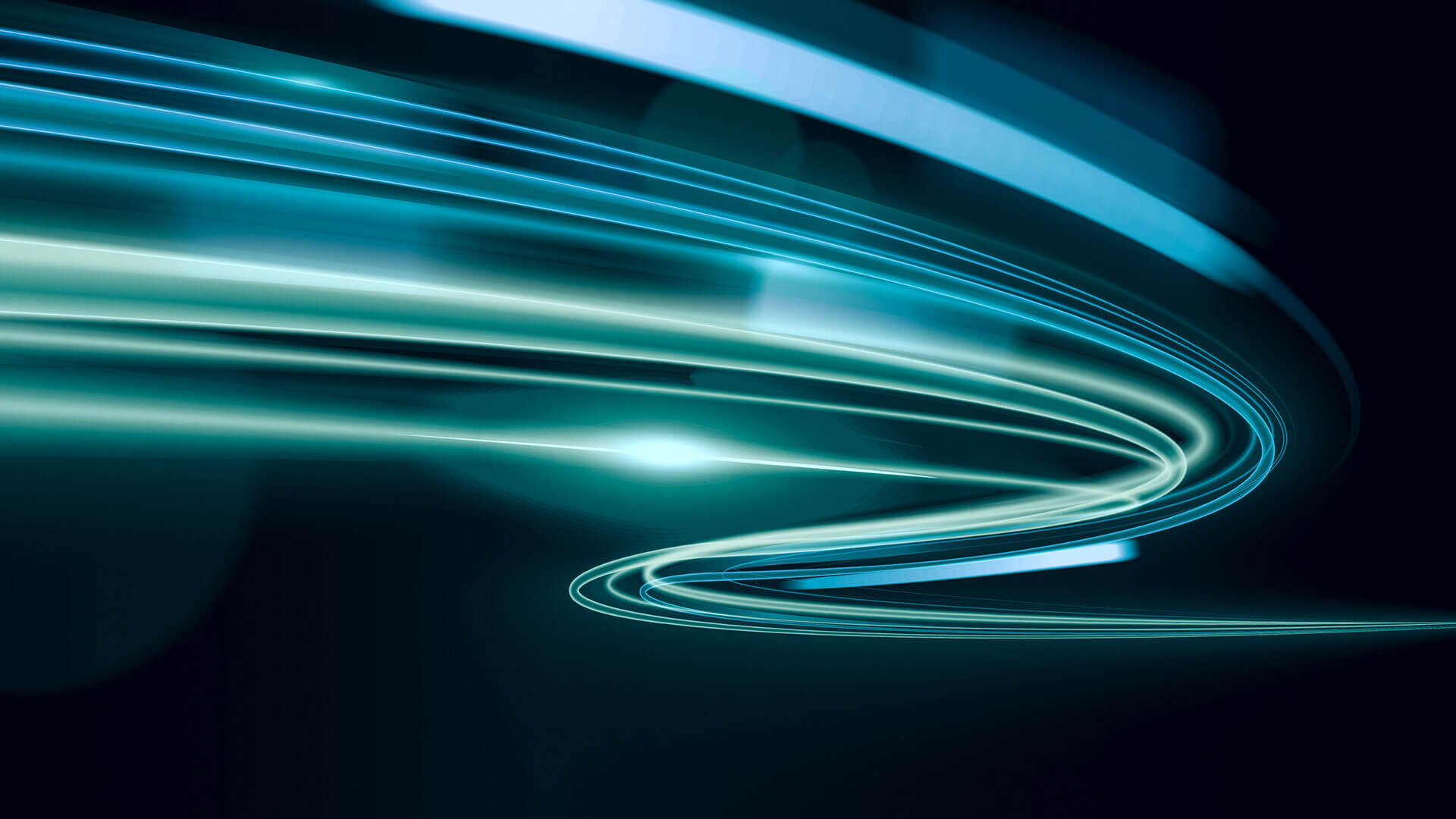
Soft sensors
Gain real-time estimates of variables that are difficult, costly, or even impossible to measure directly using AI.
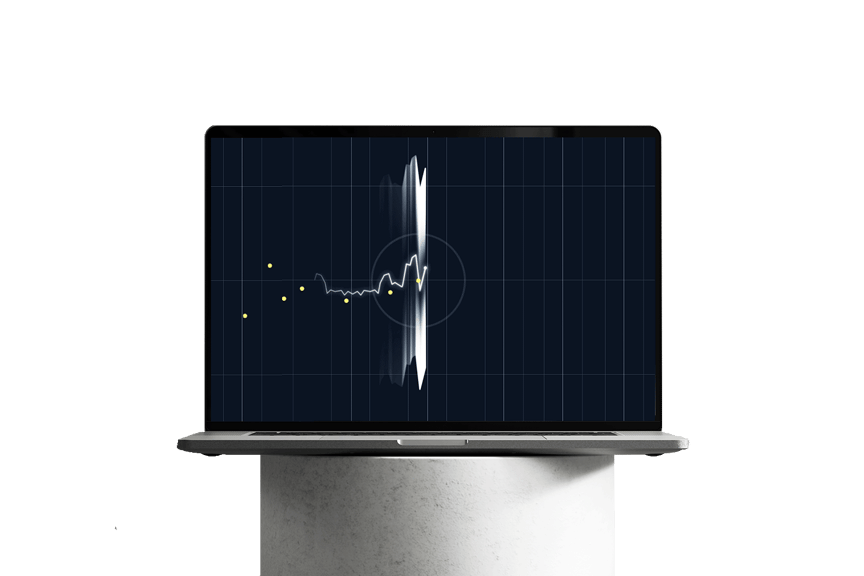
See the future
Understanding every aspect of your production process is key to staying ahead. Waiting for that lab result to come out to determine whether or not a product is viable is simply too late. FH Soft sensors enable you to:
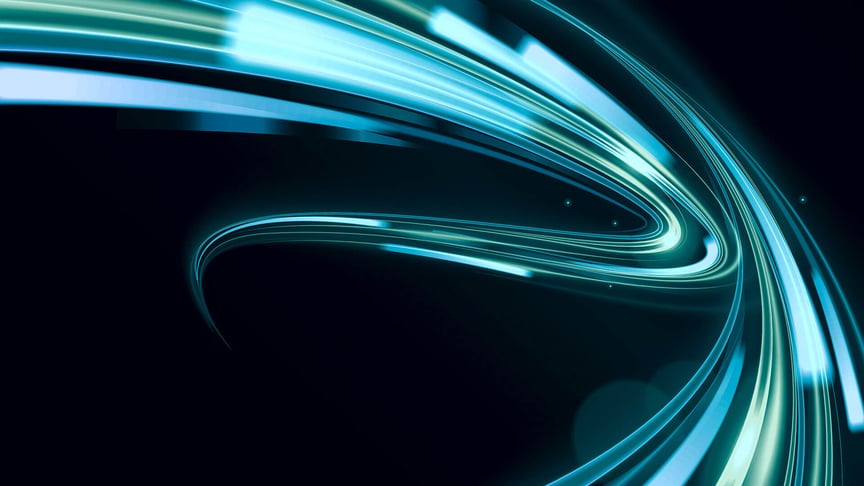
How soft sensors work
Soft sensors are built by combining process knowledge with advanced data analytics. Here’s how we do it:
Use case example
Chemical Production
Soft sensors enable real-time estimation of critical quality parameters such as pH levels, temperatures, pressures, and raw material and energy consumptions. This allows for more efficient production processes, reducing waste and operational costs, and improving overall product quality and yield.
use case example
Pulp and Paper
Soft sensors provide precise monitoring of e.g. moisture content and other key factors critical to the papermaking process. By enabling tighter control over these variables, they help maintain consistent product quality, minimize material waste, and improve energy efficiency across production stages.
Use case example
Metal Industry

Overcoming Common Challenges
While the benefits of soft sensors are clear, successful implementation requires careful planning and execution. At SimAnalytics, we address the challenges of soft sensor design by:
Soft sensor Insights
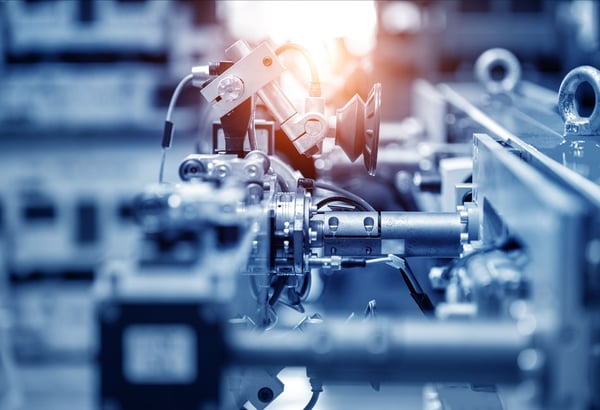
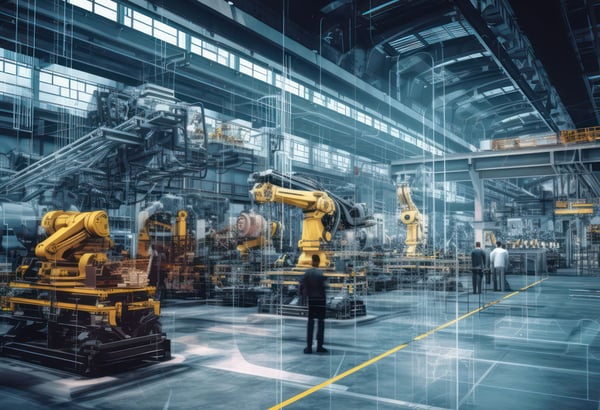
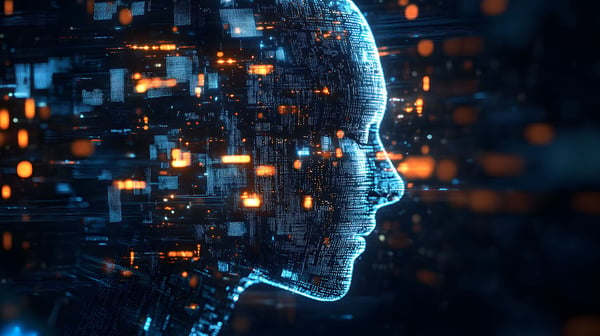
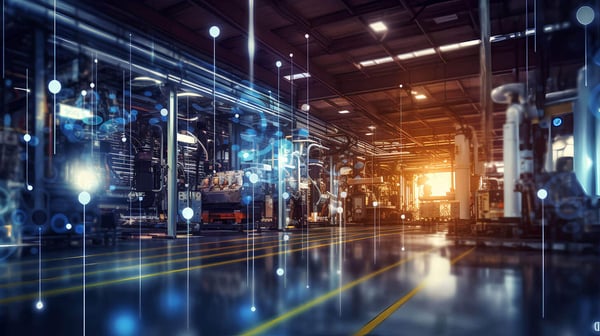
Ready to have a quick chat?
Our experts are here to assist you on your mission to improve your production processes.