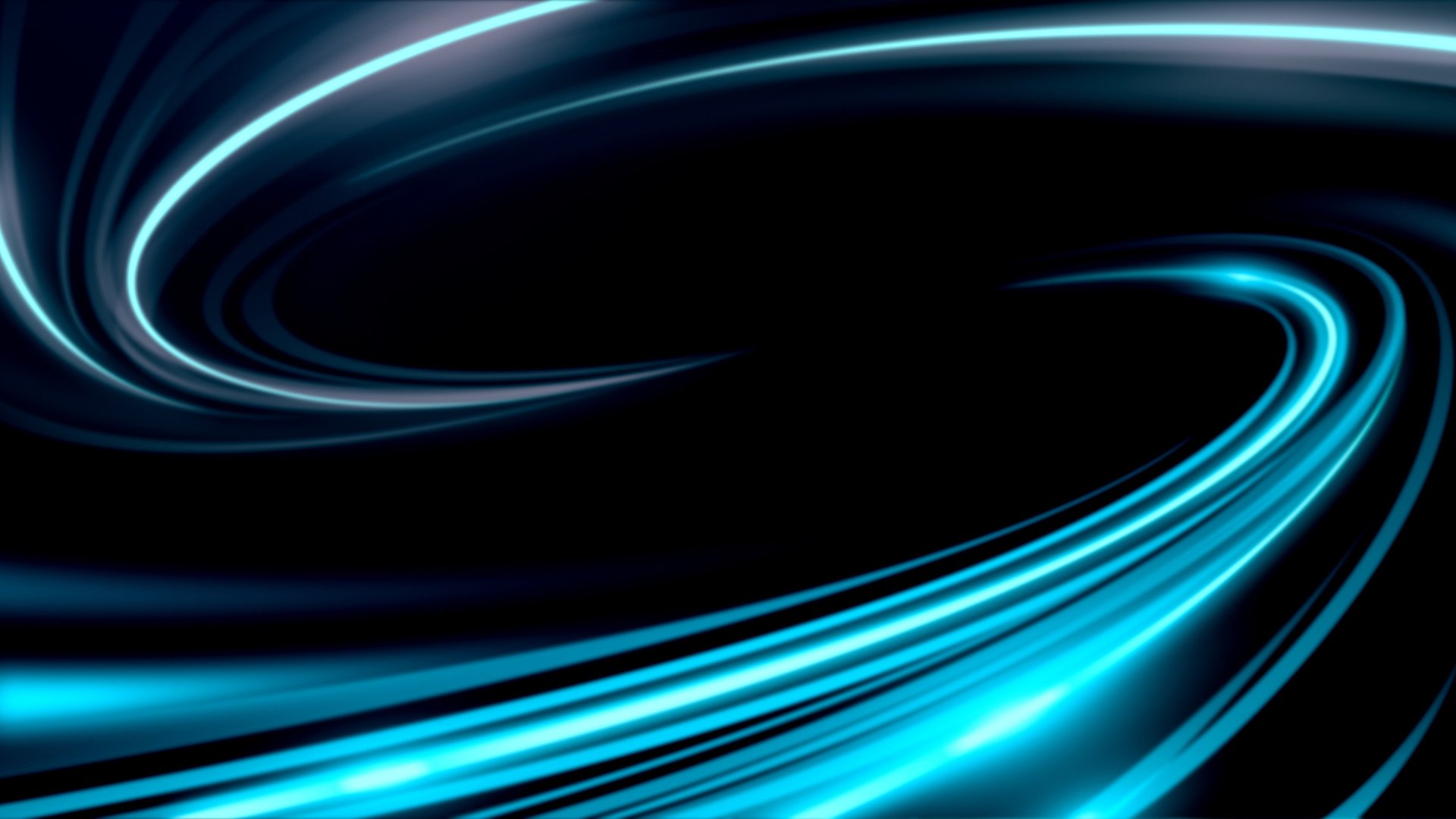
Harmony
Monitor and facilitate process harmony to enhance production stability and efficiency of complex production processes.
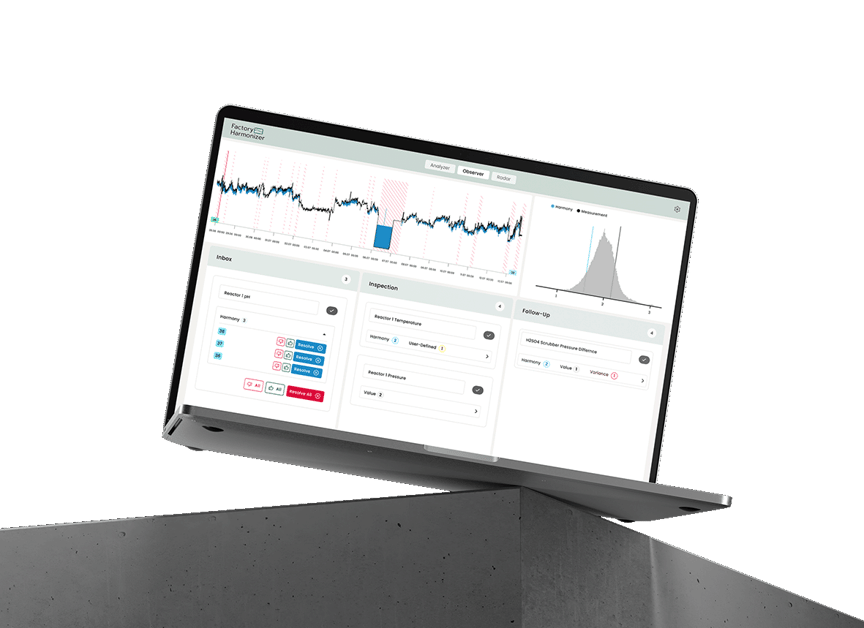
Turn data into insights
Your production data is full of valuable insights—Factory Harmonizer’s Harmony module helps you find them, even in the most complex of production processes. By simplifying complex data and presenting it visually, it makes it easy to spot root causes of disturbances and improve efficiency. With real-time monitoring and automated detection of emerging issues, you can spend less time troubleshooting and more time optimizing your process.
increased annual production profit
new annual energy savings for one production line
average payback time
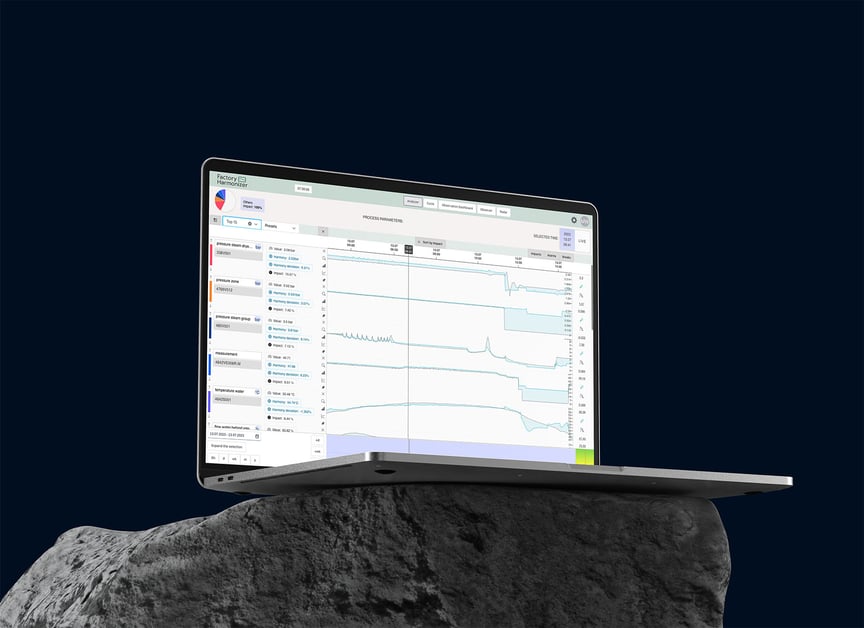
Become harmonized by harmony modelling
Harmony modelling is the brains behind FH Harmony. Unlike traditional modelling methods relying on single-point measurements and setpoint-triggered alarms, harmony modelling is able to consider interdependencies among hundreds of values. Harmony modelling offers new insights for more effective corrective and preventive actions in the dynamic landscape of modern manufacturing.
Our promise
Transparency
FH Harmony provides you with real-time insights and clear visibility of your holistic production processes at all times. Our automated model maintenance ensures that everything is always up-to-date.
Your goal
Efficiency
With FH Harmony, you will discover novel ways to improve your production processes and understand the root causes behind process disturbances at ease. Spend less time on false alarms and more on what truly matters.
our vision
Harmony
Keep operations running smoothly and get the most out of your production. Spot opportunities to increase yield, improve product quality, and make daily work easier for your team with actionable insights.
Module views
Managing intricate production processes, which involve thousands of variables with scattered data most often stored in historians, can be challenging. FH Harmony simplifies this complexity to provide improved visibility and control, presented to users in four distinct and user-friendly views for complete clarity.
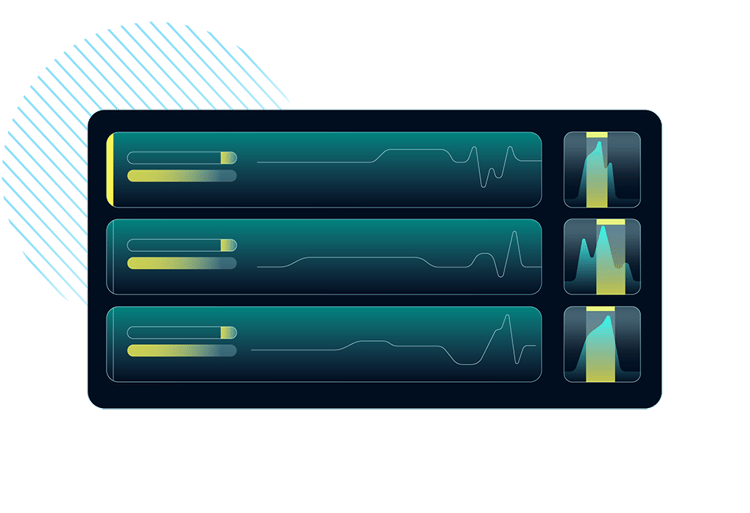
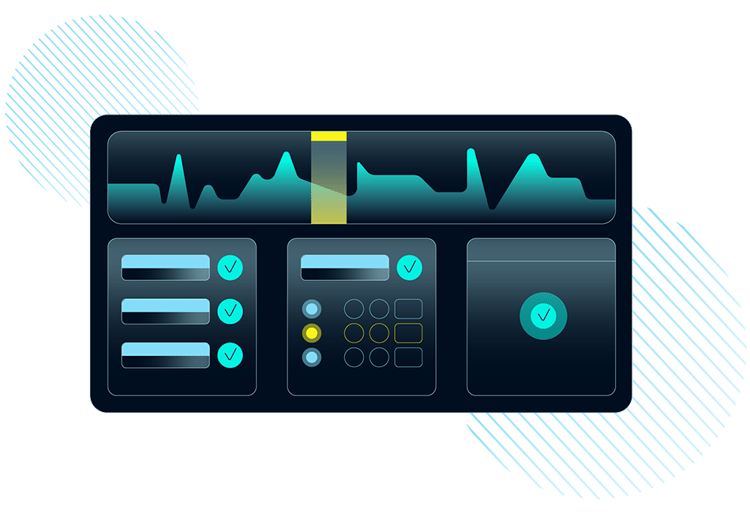
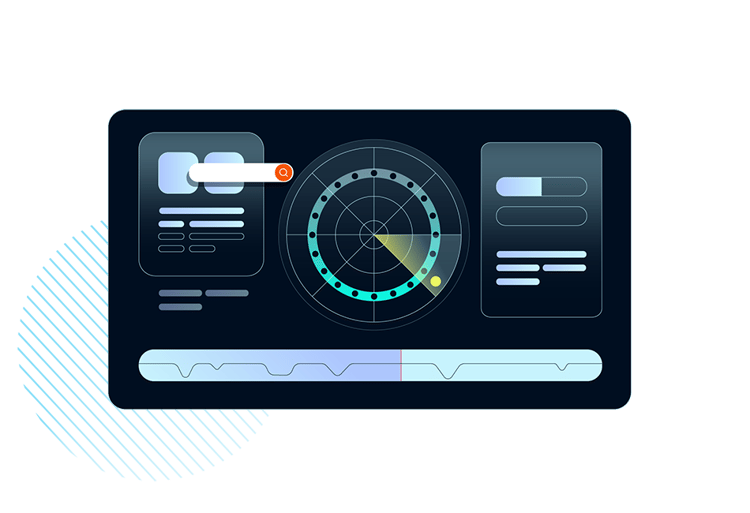
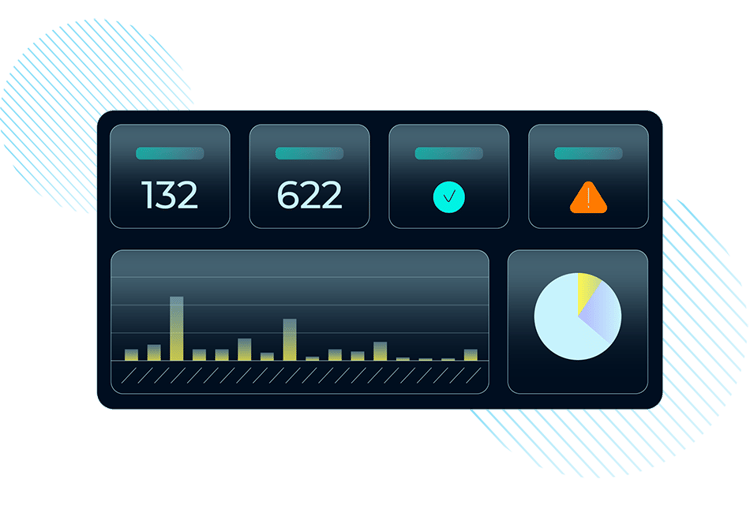
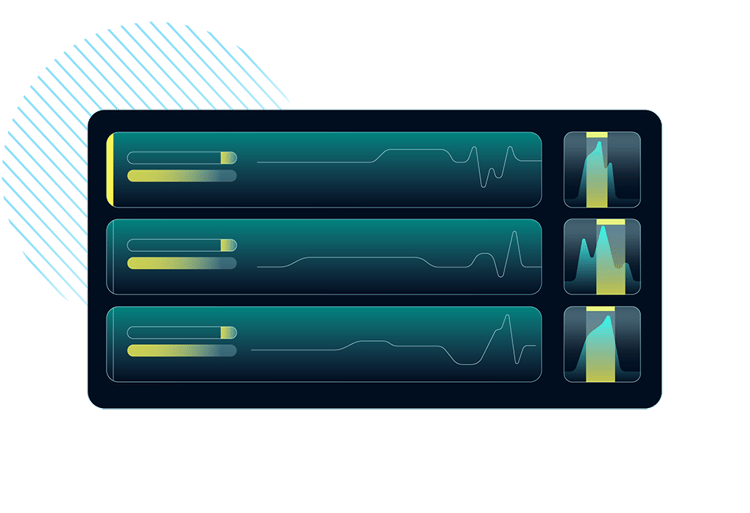
Identify, analyze, and drill down to uncover the root cause of process deviations. Proactively detect potential disruptions and evaluate their impact on process stability for swift corrective actions.
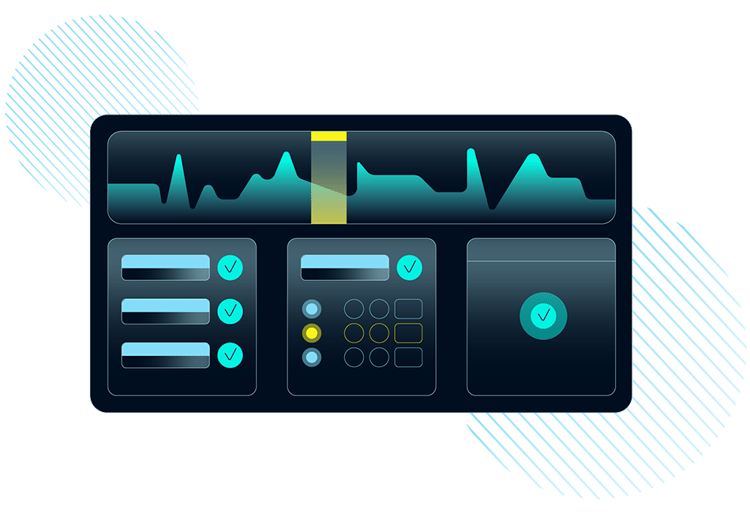
Prioritizes the most crucial process deviations, offering a clear view to systematically facilitate necessary changes across your team. Observer ensures you focus on key areas, fostering efficiency and timely responses.
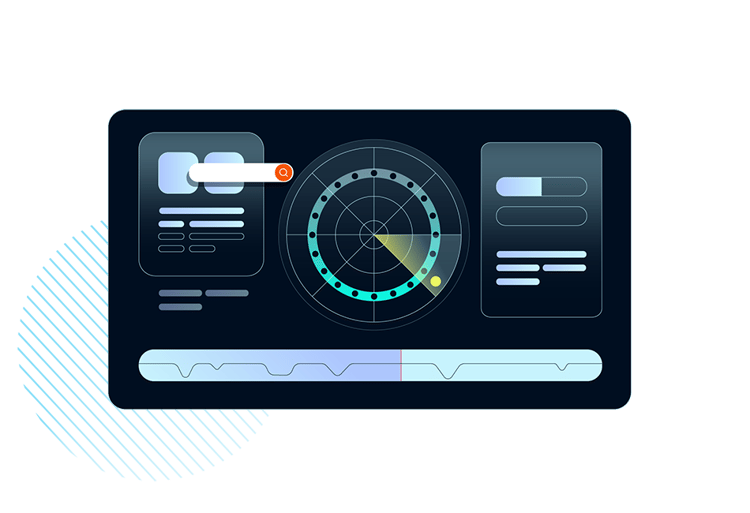
Immediately identify deviations in process settings from their usual values. Utilizing histogram analysis, swiftly assess whether these exceptional set-points fall within acceptable limits, enabling prompt corrective action.
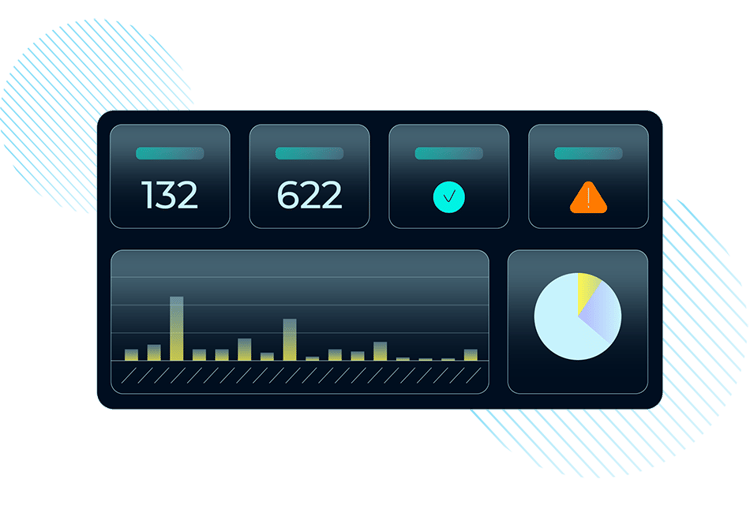
Obtain visibility into essential KPIs in a single view to track ongoing processes and monitor the impact of corrective actions on production efficiency. Dashboard simplifies your operational overview, aiding informed decision-making.
Your production is our priority
We prioritize minimizing the time commitment from your key personnel without compromising essential work. In comparison to other tools on the market, we take care of all the modelling and re-modelling for you so that you can focus on the actionable insights gained.
Our projects begin with a structured 3–4-month pilot aimed at exploring the latent possibilities of Factory Harmonizer using the customer's own historical production data. During the pilot, we'll need to borrow just a couple of days of your experts' time. Read more about the offline pilot.
Factory Harmonizer offers a user-friendly interface designed for easy navigation, allowing users to quickly access critical information without the need for extensive training. The platform’s dashboards are intuitive and customizable, making it simple for operators, engineers, and managers to find the insights they need to make informed decisions. This ensures that your team can efficiently manage production processes with minimal friction.
Factory Harmonizer seamlessly integrates with a variety of Distributed Control Systems (DCS) and historian databases from automation system data providers like Valmet, Siemens, Honeywell, ABB, OSIsoft/AVEVA, or Oracle. These databases can be augmented with additional data sources, such as laboratory data, for comprehensive analysis. Additionally, Factory Harmonizer can incorporate data from other systems like Manufacturing Control Systems (MCS) or Quality Management Systems (QMS) if available.
We are proud to be ISO 27001 certified, ensuring that Factory Harmonizer meets the highest standards for information security. This certification reflects our commitment to safeguarding your data, minimizing risks, and continuously improving our security practices. With ISO 27001 in place, you can trust that your sensitive production data is managed and protected with the utmost care.
Concerned about the quality and volume of your data? Rest assured, we take full responsibility for ensuring that the data driving your decisions is both accurate and reliable. Before deployment, our team conducts a meticulous screening process to verify the integrity and feasibility of the available data. This includes a comprehensive Data Health Check, where we sift through and evaluate all collected data to ensure that only relevant, high-quality information is integrated into the system. By optimizing the accuracy and reliability of the data used, we enhance the effectiveness of Factory Harmonizer's models, providing you with trustworthy insights and actionable results that drive your operations forward.
Factory Harmonizer is designed to stay ahead of your evolving needs with automatic updates and continuous model enhancements. The system receives regular updates that introduce new features and improvements without interrupting your workflow. Additionally, Factory Harmonizer’s models undergo automated re-training at regular intervals, ensuring they adapt to changes in your production environment without requiring system breaks or incurring additional costs.
Factory Harmonizer is engineered for fast and reliable data processing, providing real-time analysis and insights that you can trust. The platform’s powerful analytics engine processes large volumes of data with speed and precision, ensuring that you receive up-to-date information without delays.
Once you decide to optimize your processes with Factory Harmonizer, you’ll be assigned a dedicated project team. This team is committed to providing personalized, effective support, ensuring that your experience with our software extends beyond just the technology itself.
During the pilot phase, we provide thorough training to equip your team with the skills they need to fully leverage the system’s features. This initial training, combined with ongoing support, ensures that your operations run seamlessly and that your team is confident and proficient in using Factory Harmonizer to its fullest potential.
After the pilot phase, you are not left alone. Our dedicated support team is ready to assist you if nay questions arise.
Ready to have a quick chat?
Our experts are here to assist you on your mission to improve your production processes.