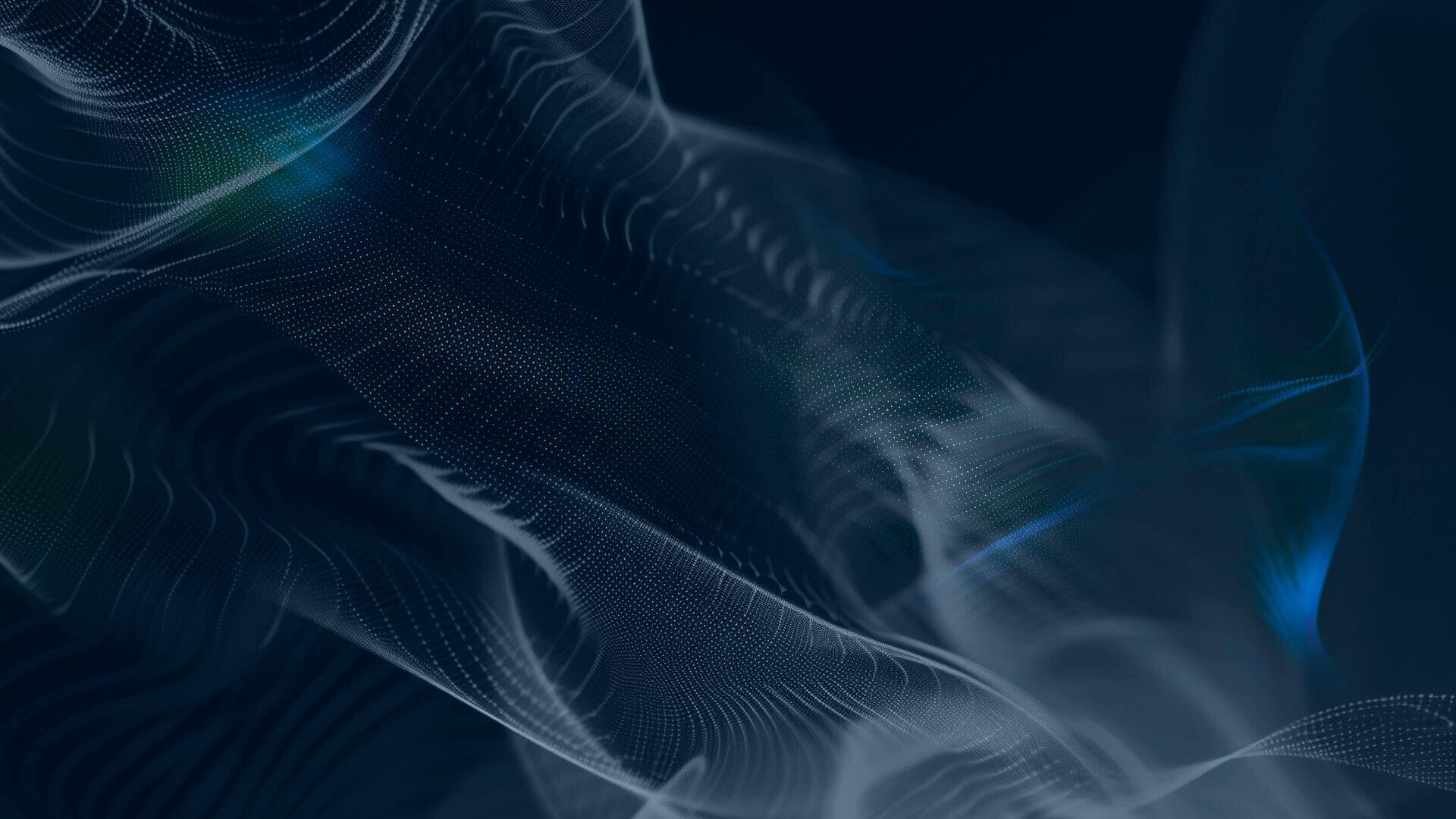
Industrial Analytics
made easy.
By blending real-time process data and automated machine learning, our advanced analytics software solution provides your experts with insights to improve efficiency, stability, and sustainability across your production processes.
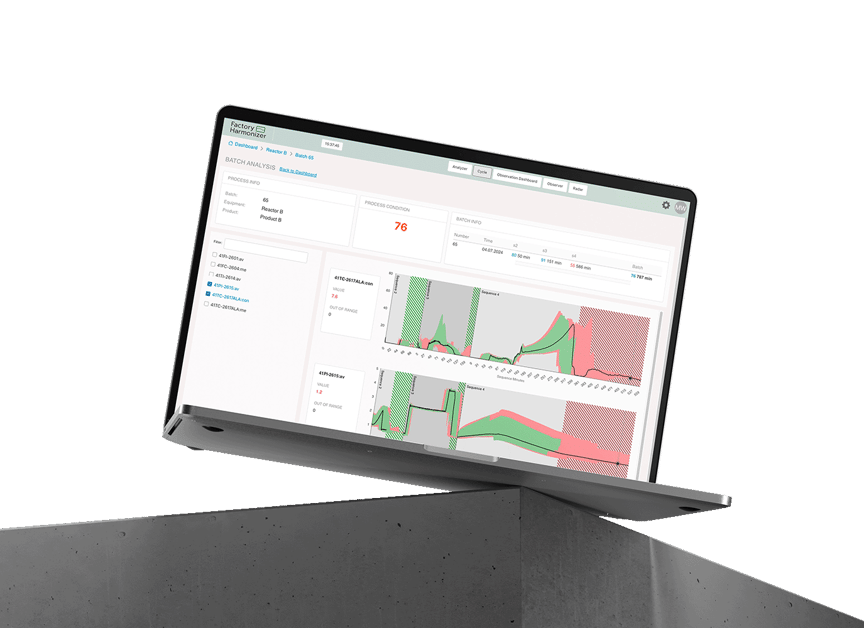
It all starts with data
Your production process data holds valuable insights. We help you uncover them by simplifying the complexity and presenting the data visually. This allows you to identify the root causes of disturbances, explore new ways to improve processes, and monitor production in real-time. Our complete solution includes our intelligent data platform, modules tailored to different use cases, customer support, and a dedicated project team ready to set you up for success.
Transparency
Get a clear view of your production in real-time. Quickly spot and resolve any issues to keep everything running smoothly.
Efficiency
Make smarter adjustments to your production process with data-driven insights. Produce more in less time and boost your profits.
Sustainability
Reduce waste and energy use by making informed decisions. Save money while meeting your sustainability goals and maintaining quality.
“Factory Harmonizer can identify hidden signals from the process, that are otherwise missed by our current systems.”
- Satisfied Customer
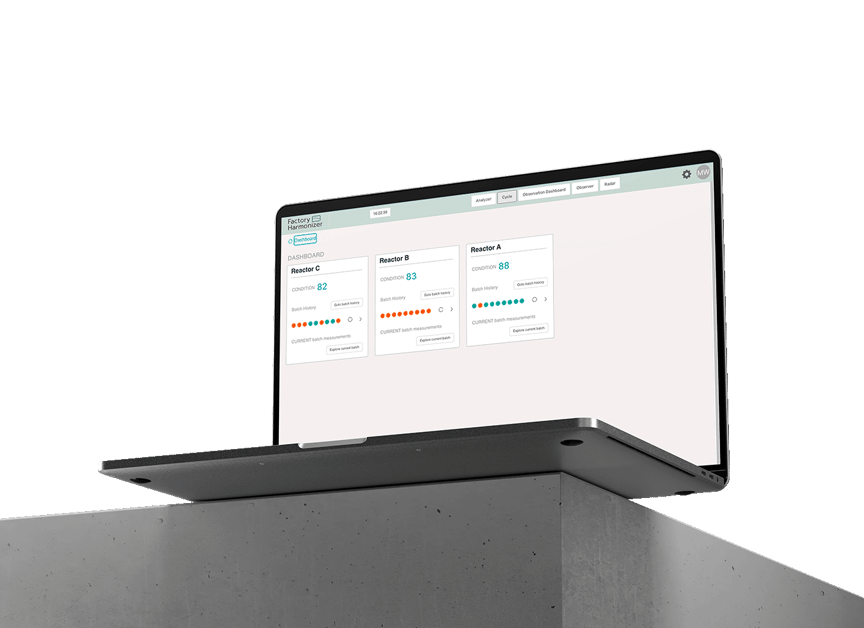
Use cases across the process industry
Our solution is tailored for operators and engineers in the process industry, offering an intuitive web-based interface designed for quick, effective insights. With carefully curated alerts and actionable insights, it ensures your team gets the information they need at just a glance—no more, no less.
Chemical Industry
Pulp & Paper
Metal Industry
Oil & Gas Production
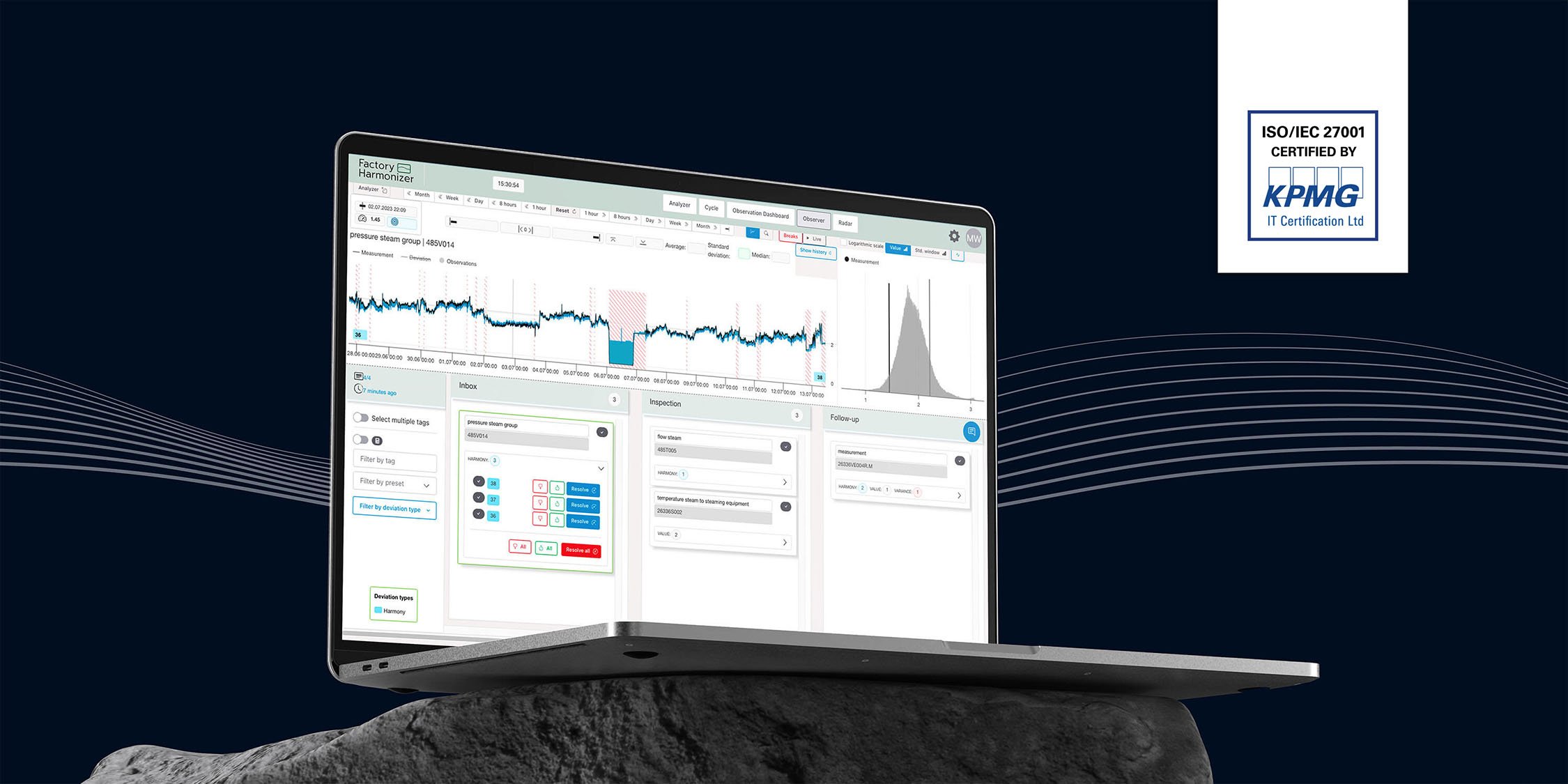
We ensure the best experience
We prioritize minimizing the time commitment from your key personnel without compromising essential work. In comparison to other tools on the market, we take care of all the modelling and re-modelling for you so that you can focus on the actionable insights gained.
Our projects begin with a structured 3–4-month pilot aimed at exploring the latent possibilities of Factory Harmonizer using the customer's own historical production data. During the pilot, we'll need to borrow just a couple of days of your experts' time. Read more about the offline pilot.
Factory Harmonizer offers a user-friendly interface designed for easy navigation, allowing users to quickly access critical information without the need for extensive training. The platform’s dashboards are intuitive and customizable, making it simple for operators, engineers, and managers to find the insights they need to make informed decisions. This ensures that your team can efficiently manage production processes with minimal friction.
Factory Harmonizer seamlessly integrates with a variety of Distributed Control Systems (DCS) and historian databases from automation system data providers like Valmet, Siemens, Honeywell, ABB, OSIsoft/AVEVA, or Oracle. These databases can be augmented with additional data sources, such as laboratory data, for comprehensive analysis. Additionally, Factory Harmonizer can incorporate data from other systems like Manufacturing Control Systems (MCS) or Quality Management Systems (QMS) if available.
We are proud to be ISO 27001 certified, ensuring that Factory Harmonizer meets the highest standards for information security. This certification reflects our commitment to safeguarding your data, minimizing risks, and continuously improving our security practices. With ISO 27001 in place, you can trust that your sensitive production data is managed and protected with the utmost care.
Concerned about the quality and volume of your data? Rest assured, we take full responsibility for ensuring that the data driving your decisions is both accurate and reliable. Before deployment, our team conducts a meticulous screening process to verify the integrity and feasibility of the available data. This includes a comprehensive Data Health Check, where we sift through and evaluate all collected data to ensure that only relevant, high-quality information is integrated into the system. By optimizing the accuracy and reliability of the data used, we enhance the effectiveness of Factory Harmonizer's models, providing you with trustworthy insights and actionable results that drive your operations forward.
Factory Harmonizer is designed to stay ahead of your evolving needs with automatic updates and continuous model enhancements. The system receives regular updates that introduce new features and improvements without interrupting your workflow. Additionally, Factory Harmonizer’s models undergo automated re-training at regular intervals, ensuring they adapt to changes in your production environment without requiring system breaks or incurring additional costs.
Factory Harmonizer is engineered for fast and reliable data processing, providing real-time analysis and insights that you can trust. The platform’s powerful analytics engine processes large volumes of data with speed and precision, ensuring that you receive up-to-date information without delays.
Once you decide to optimize your processes with Factory Harmonizer, you’ll be assigned a dedicated project team. This team is committed to providing personalized, effective support, ensuring that your experience with our software extends beyond just the technology itself.
During the pilot phase, we provide thorough training to equip your team with the skills they need to fully leverage the system’s features. This initial training, combined with ongoing support, ensures that your operations run seamlessly and that your team is confident and proficient in using Factory Harmonizer to its fullest potential.
After the pilot phase, you are not left alone. Our dedicated support team is ready to assist you if nay questions arise.
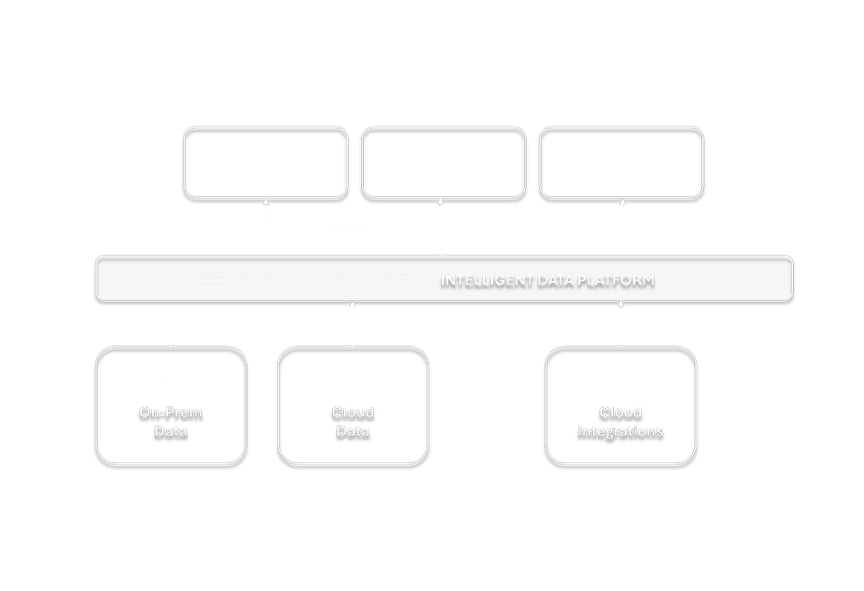
Each production process is unique
To meet the unique requirements of the production processes we have developed three distinct modules. The modules work seamlessly on top of the Factory Harmonizer Data Platform. The Data Platform ensures that all your production line data is collected from your systems, processed, and monitored in one place.
FH Cycle
Streamline batch process control with real-time insights into the condition of your batch production. Enhance process efficiency and ensure optimal product quality.
FH Harmony
Boost production stability and efficiency by monitoring and identifying process deviations that go beyond your regular check-ups. Made for complex processes.
FH Soft sensors
Generate continuous values for challenging or costly variables such as lab measurements, to save time and resources, and to proactively control your process.
Ready to have a quick chat?
Our experts are here to assist you on your mission to improve your production processes.