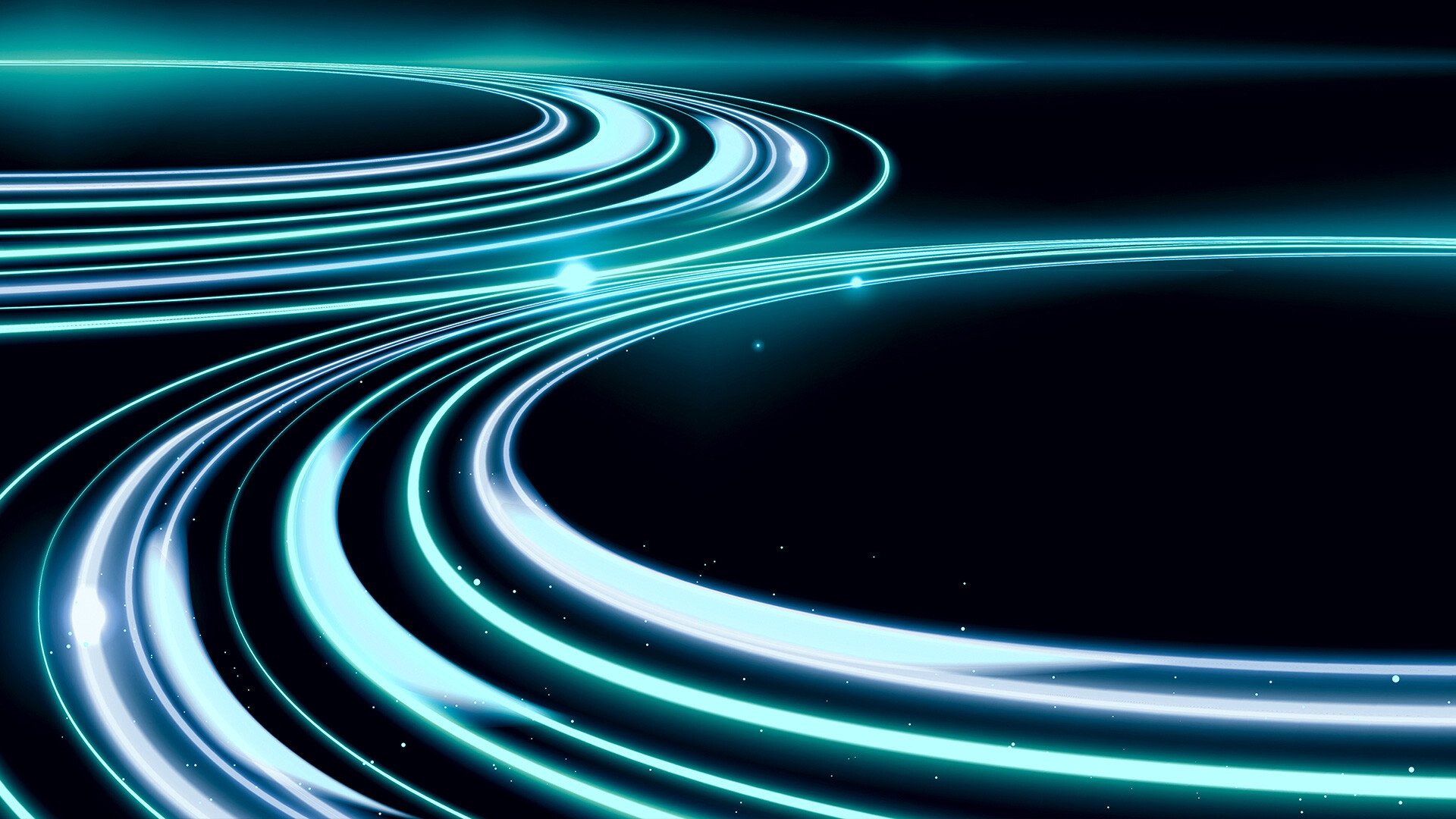
Cycle
Streamline your process control with real-time insights into your batch production's current and historical condition.
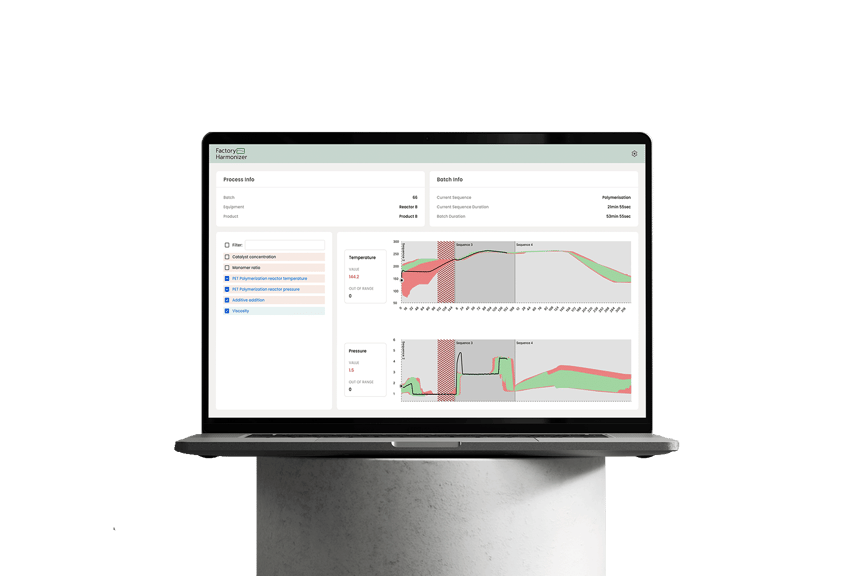
Make data work for you
Your batch production data is the key ingredient to helping you produce the right quality in just the right amount of time for optimal production. Factory Harmonizer's Cycle module directly supports your operators in making swift changes to your ongoing batch, while providing your process engineers with a comprehensive view into past runs.
Our promise
Consistency
FH Cycle provides you with instant access to the insights needed to keep production on track, empowering operators to manage processes confidently and achieve better, more consistent results.
Our promise
Continuous improvement
With FH Cycle, swiftly identify improvement opportunities and understand the condition of your processes. Test out new ways of working and make significant improvements to your KPIs.
Our promise
Productivity
Gain visibility into the state of your production to reduce downtime, speed up cycles, and generate less faulty products, making your operations more responsive and efficient.
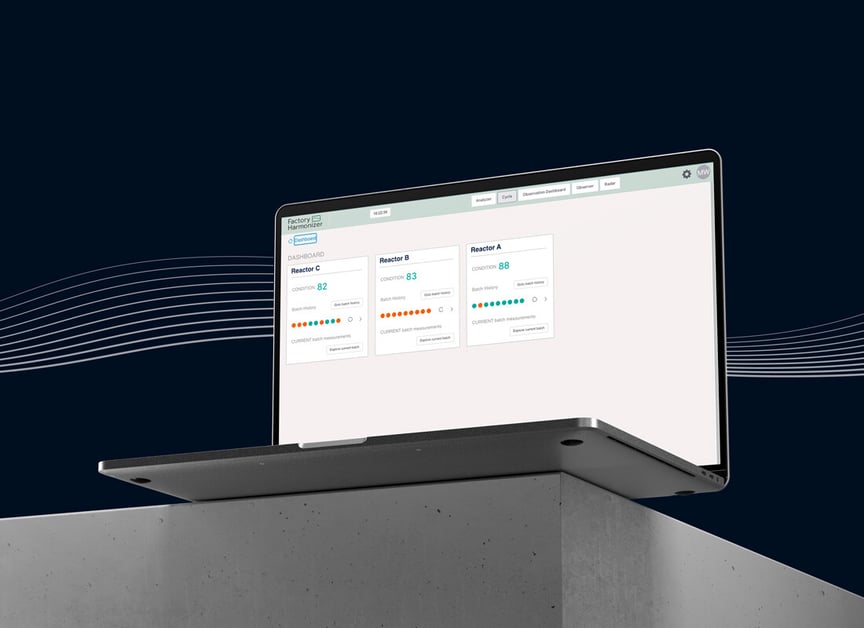
Unique approach
FH Cycle is tailored to provide operators and engineers with actionable insights into batch production processes in real-time without requiring any previous knowledge of data engineering.
Our wish is to automate where possible and let our software build all models for you so that you can focus your time on running your production. In addition to saving time and sparing the cost of hiring an expensive data scientist, automated model building helps to maintain optimal model performance without constant and costly intervention.
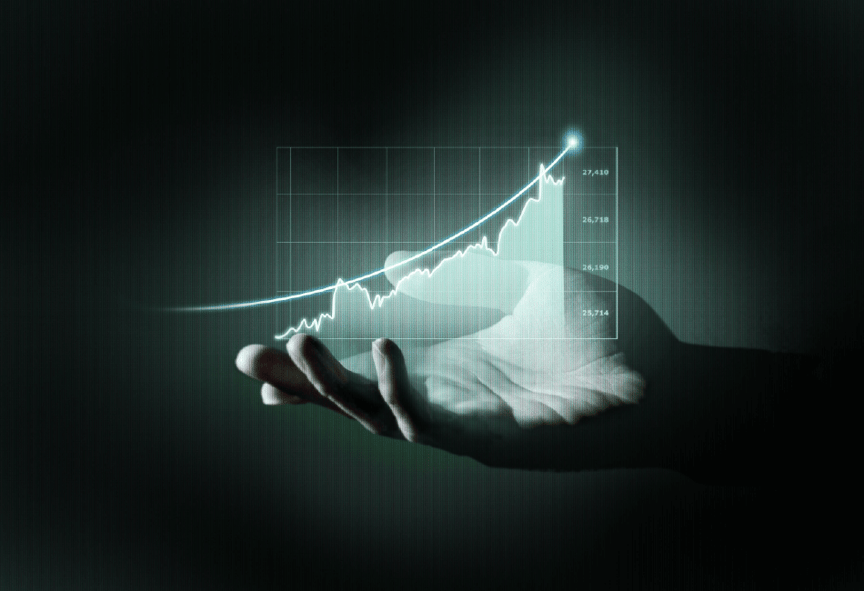
Webinar: Controlling Batch Cycles
In this 40-minute on-demand webinar, Eero Peiponen, Development Manager at Kemira explores key challenges in controlling batch cycles, followed by Samuli Kortelainen who provides insights into how analytics can help address these challenges.
Module views
FH Cycle simplifies real-time process control and provides enhanced visibility and control through three intuitive views, empowering operators and process engineers with actionable insights for optimized operations. With FH Cycle, users gain a comprehensive overview of historical and current batches, making it easier to drive efficiency, ensure optimal product quality, and focus on continuous improvement.

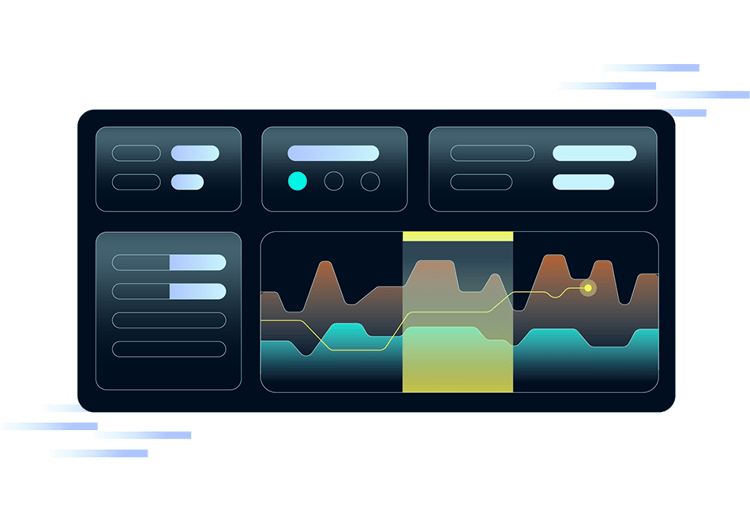
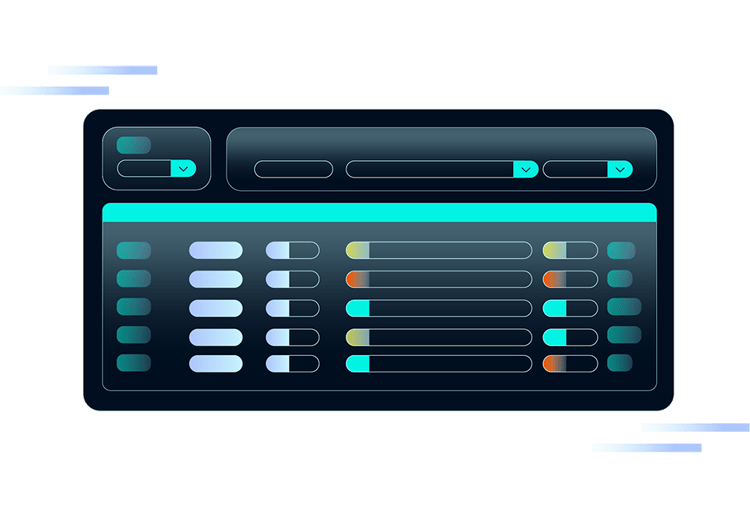

Always dreamt of having a one-screen overview of your batch production? Look no further. Equipment cards provide quick insights into the state of the equipment, the current state of production thereof as well as a quick historical overview of batches and sequences.
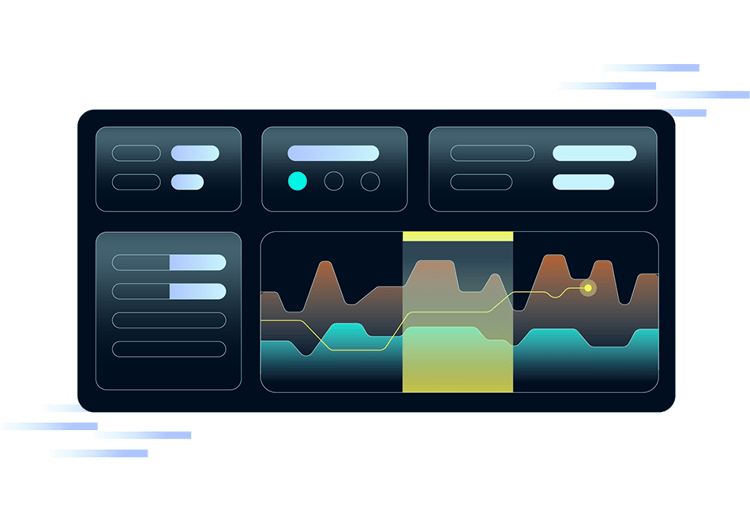
Our unique intelligent operational windows are automatically calculated and defined for each measurement using historical batch data. These windows enable operators to adjust measurements, ensuring they remain within the optimal range and don't slip outside of the green zone.
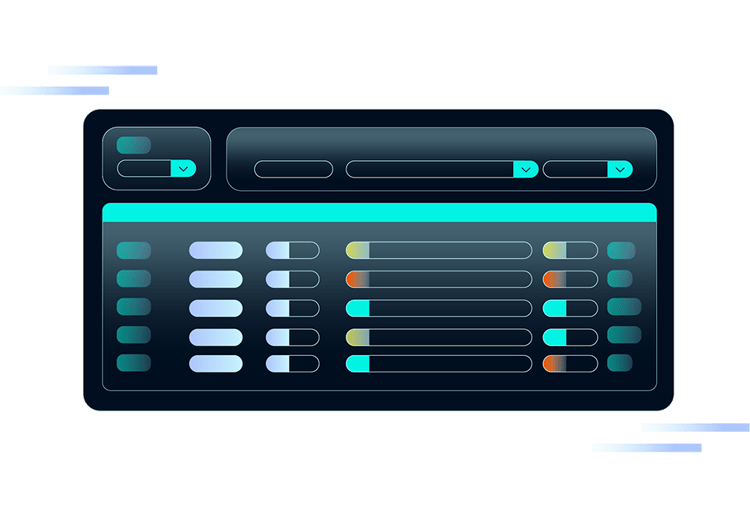
Filter by product to view cycle and sequence times for each batch. Drill down to discover what measurements have impacted performance and find ways to improve overall production efficiency.
Your production is our priority
We prioritize minimizing the time commitment from your key personnel without compromising essential work. In comparison to other tools on the market, we take care of all the modeling and re-modeling for you so that you can focus on the actionable insights gained.
Our projects begin with a structured 3–4-month pilot aimed at exploring the latent possibilities of Factory Harmonizer using the customer's own historical production data. During the pilot, we'll need to borrow just a couple of days of your experts' time. Read more about the offline pilot.
Factory Harmonizer offers a user-friendly interface designed for easy navigation, allowing users to quickly access critical information without the need for extensive training.
Factory Harmonizer seamlessly integrates with a variety of Distributed Control Systems (DCS) and historian databases from automation system data providers like Valmet, Siemens, Honeywell, ABB, OSIsoft/AVEVA, or Oracle. These databases can be augmented with additional data sources, such as laboratory data, for comprehensive analysis. Additionally, Factory Harmonizer can incorporate data from other systems like Manufacturing Control Systems (MCS) or Quality Management Systems (QMS) if available.
We are proud to be ISO 27001 certified, ensuring that Factory Harmonizer meets the highest standards for information security. This certification reflects our commitment to safeguarding your data, minimizing risks, and continuously improving our security practices. With ISO 27001 in place, you can trust that your sensitive production data is managed and protected with the utmost care.
Concerned about the quality and volume of your data? Rest assured, we take full responsibility for ensuring that the data driving your decisions is both accurate and reliable. Before deployment, our team conducts a meticulous screening process to verify the integrity and feasibility of the available data. This includes a comprehensive Data Health Check, where we sift through and evaluate all collected data to ensure that only relevant, high-quality information is integrated into the system. By optimizing the accuracy and reliability of the data used, we enhance the effectiveness of Factory Harmonizer's models, providing you with trustworthy insights and actionable results that drive your operations forward.
Factory Harmonizer is designed to stay ahead of your evolving needs with automatic updates and continuous model enhancements. The system receives regular updates that introduce new features and improvements without interrupting your workflow. Additionally, Factory Harmonizer’s models undergo automated re-training at regular intervals, ensuring they adapt to changes in your production environment without requiring system breaks or incurring additional costs.
Factory Harmonizer is engineered for fast and reliable data processing, providing real-time analysis and insights that you can trust. The platform’s powerful analytics engine processes large volumes of data with speed and precision, ensuring that you receive up-to-date information without delays.
Once you decide to optimize your processes with Factory Harmonizer, you’ll be assigned a dedicated project team. This team is committed to providing personalized, effective support, ensuring that your experience with our software extends beyond just the technology itself.
During the pilot phase, we provide thorough training to equip your team with the skills they need to fully leverage the system’s features. This initial training, combined with ongoing support, ensures that your operations run seamlessly and that your team is confident and proficient in using Factory Harmonizer to its fullest potential.
After the pilot phase, you are not left alone. Our dedicated support team is ready to assist you if nay questions arise.
Ready to have a quick chat?
Our experts are here to assist you on your mission to improve your production processes.